"When AI Designs Components, They Sometimes Defy Textbook Engineering": Space Force's Lt. Col. Thomas Nix on Additive Manufacturing, Materials Science, and the Race to Develop Nuclear Propulsion by 2030
Space Force's Lt. Col. Thomas Nix leads a $70M program developing AI-designed nuclear propulsion systems that could halve travel time to Mars by 2030, overcoming space's unique heat management challenges through innovative materials and manufacturing.
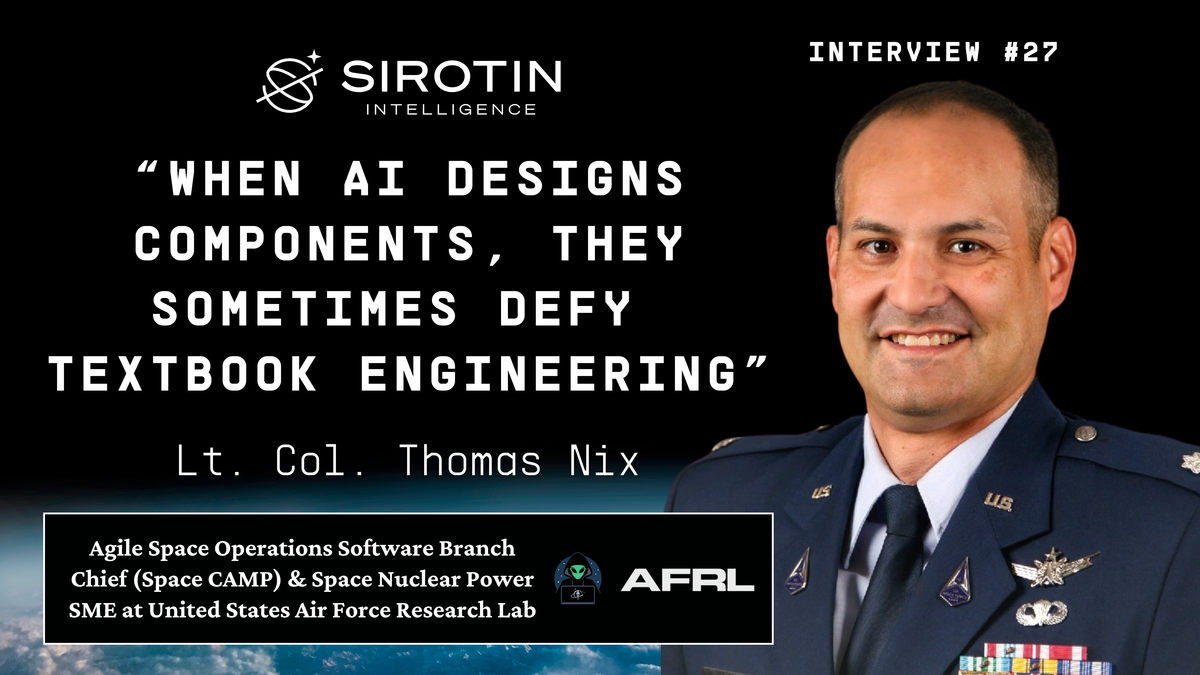
The screen flickers as impossibly complex geometries take shape—components designed by artificial intelligence that, according to conventional engineering textbooks, should collapse under pressure. Yet when manufactured and tested, these strange structures outperform traditional designs. This is the frontier where Lieutenant Colonel Thomas Nix operates.
"When AI designs components, they sometimes defy textbook engineering," explains the Space Force officer leading a $70 million program to harness nuclear power in space. The stakes are enormous: nuclear propulsion could cut travel time to Mars in half and transform humanity's relationship with the cosmos. But first, engineers must solve a deceptively simple problem that has thwarted progress for decades—managing extreme heat in the vacuum of space, where conventional cooling doesn't work.
The journey from wide-eyed six-year-old at the Smithsonian to Space Force Lieutenant Colonel wasn't what Nix imagined when he first gazed at those rocket exhibits. Now he races to develop nuclear propulsion by 2030, pushing the boundaries of what's possible beyond Earth.
What initially sparked your interest in space and led you to pursue a career in this field?
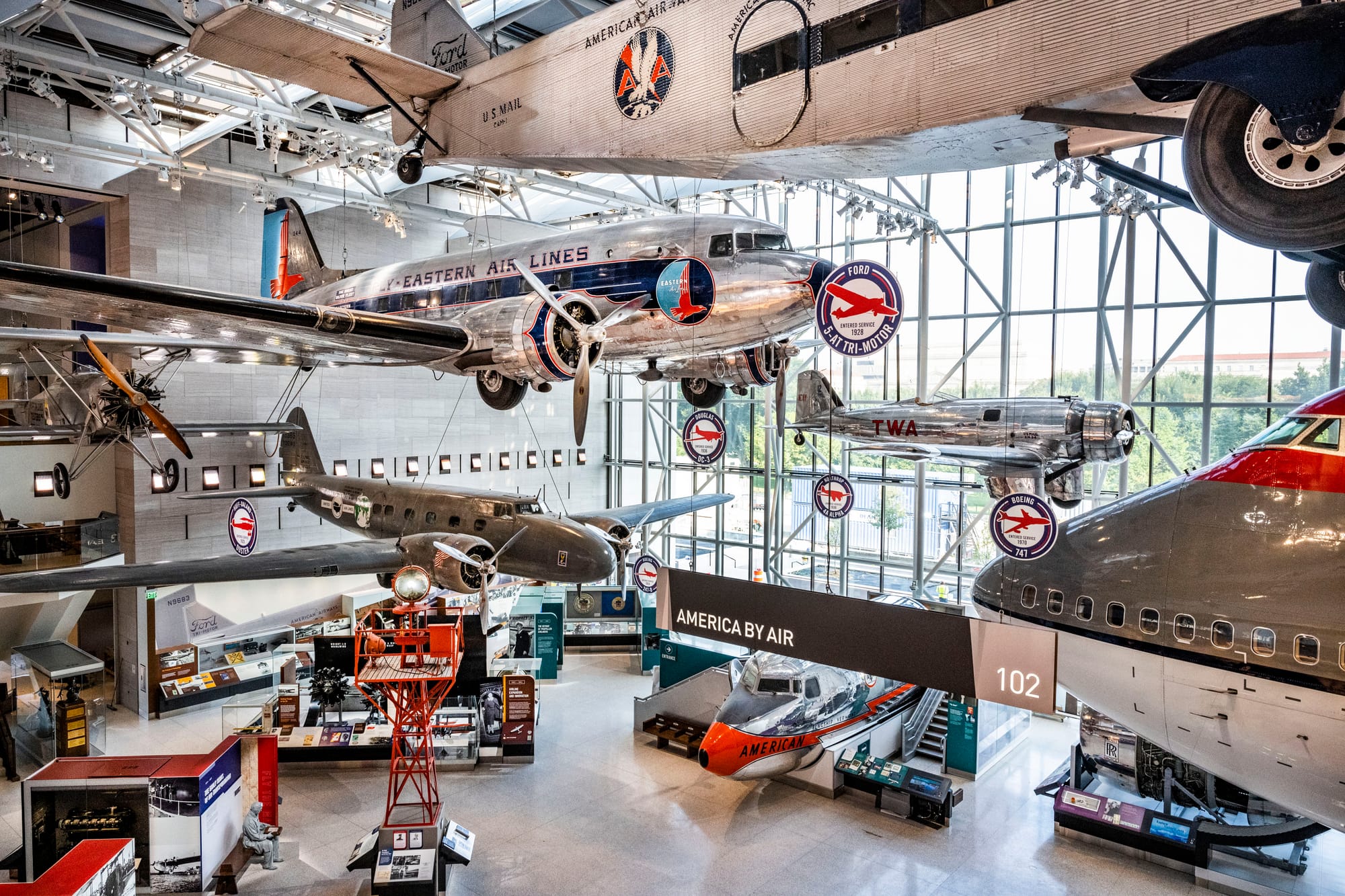
"My parents took me to the Smithsonian Air and Space Museum when I was 6 years old and I was completely hooked on Aerospace," Nix recalls, describing an experience that would shape countless others like him. The museum, which houses iconic artifacts including the Wright Flyer and Apollo 11 command module, welcomes approximately 8 million visitors annually and often ignites the first spark of aerospace passion in young minds. "We went to an air show at Oceana Naval Air Station, and then to the Smithsonian a couple weeks after that. I wanted to know who gets to build these airplanes and rockets, and my dad said, 'You have to be an aerospace engineer.' That's when I decided that's what I would do for the rest of my life."
The path forward became clear for young Nix after his family relocated. "After moving to Florida, I got to go out to the Cape for NASA and Air Force launches. I pursued an Aero/Mech double major at the Air Force Academy with a minor in math, followed by a master's degree in Astro and thermodynamics. After a brief stint in pilot training, I was lucky enough to go to my first assignment at the Air Force Research Laboratory and have been working on great programs ever since."
Given your background in GPS systems and now nuclear propulsion, what do you see as the most challenging technical hurdles in developing reliable nuclear power systems for long-duration space missions?
"On the technical side, the biggest hurdle to overcome is heat and how to move it around and do work," Nix explains, highlighting a challenge that has plagued space nuclear power since SNAP-10A—the first U.S. nuclear reactor launched into space in 1965. That pioneering system operated for just 43 days, generating approximately 500 watts before an electrical failure, but provided critical data that continues to inform current designs. "The reactor physics is known—once it gets to temperature, modern reactors are set to load follow. Getting the heat out to the power conversion system is both a fluids and materials challenge."
Nix puts today's challenges in historical context: "Throughout history, we've launched nuclear-powered spacecraft—the U.S. was the first country to do so in 1965 with SNAP-10A (Systems for Nuclear Auxiliary Power). We've had multiple programs since then, but many ran out of funding. Previously, we couldn't launch enough weight to solve the shielding problem, but now with heavy launch vehicles like Starship and Falcon Heavy, we can launch heavier satellites."
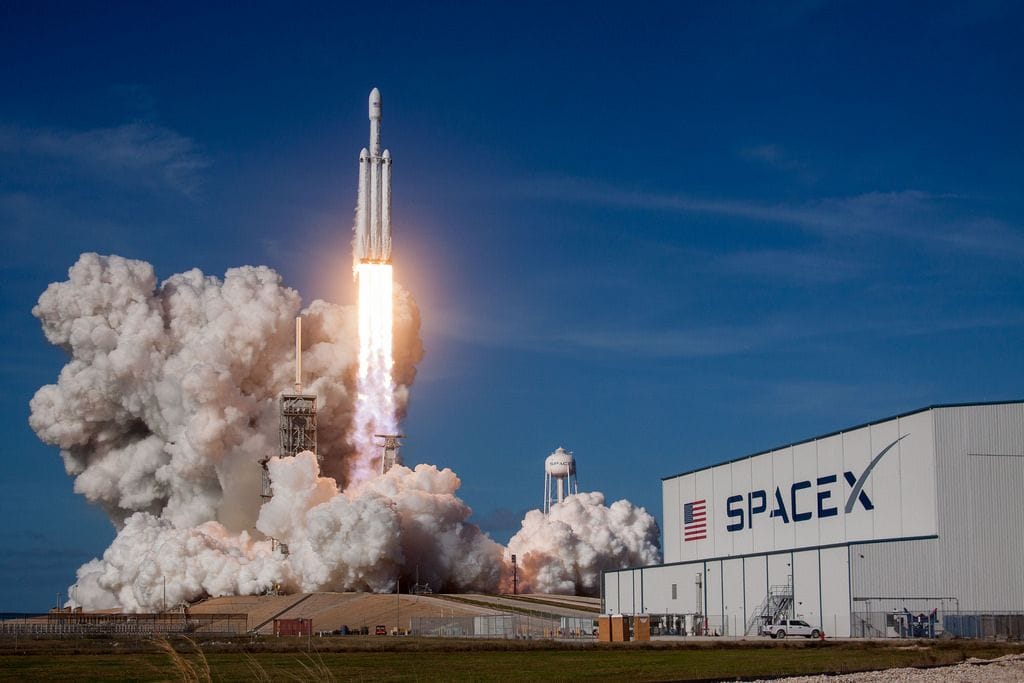
The core problem, as Nix describes it, comes down to thermodynamics in the vacuum of space. "When you look at the problem on the space side of nuclear, it's the heat. Nuclear reactors operate at 800-900 degrees centigrade, and you've got to pull that heat out to a power conversion system—whether Stirling, Rankine, or Brayton cycles."
These power conversion systems—representing different methods for transforming thermal energy into electricity—each offer distinct efficiency characteristics and trade-offs. The Stirling cycle utilizes gas compression and expansion within sealed pistons; the Rankine cycle (common in terrestrial power plants) harnesses phase changes between liquid and vapor; and the Brayton cycle (used in jet engines) compresses air, heats it, and expands it through turbines. But as Nix points out, "These systems are only 20-40% efficient, so if you're generating 400 kilowatts of thermal energy to get 100 kilowatts of electricity, you have 300 kilowatts of heat to dissipate."
"In space, there's no easy way to remove heat—you have to radiate it out as there's no convection," Nix continues, highlighting the fundamental difference between cooling on Earth versus in orbit. "So the solar panels you're trying to replace with nuclear power end up being replaced by equally large radiators. The big technological challenge is increasing the temperature of radiator materials so we can dissipate more heat in a smaller package."
What do you view as the most promising nuclear propulsion technologies for extending human presence beyond Low Earth Orbit, and what timeline do you realistically envision for their operational deployment?
"That's a tough question," Nix acknowledges, considering the complex trade-offs involved. "I believe to extend human presence past LEO, the most promising advancement is Nuclear Electric Propulsion, or more precisely, Nuclear Power Generation. The ability to generate large amounts of power in a compact design for extended periods enables operations—whether research or maneuvers—with an efficient method to station-keep and move freely."
Nix outlines the fundamental approaches that engineers are pursuing: "There are two schools of thought: Nuclear Electric Propulsion, which uses electricity from nuclear reactors to shoot ions from a thruster with super high efficiency (around 90%) but very low thrust, meaning you can move for a very long time but it takes a while to get anywhere."
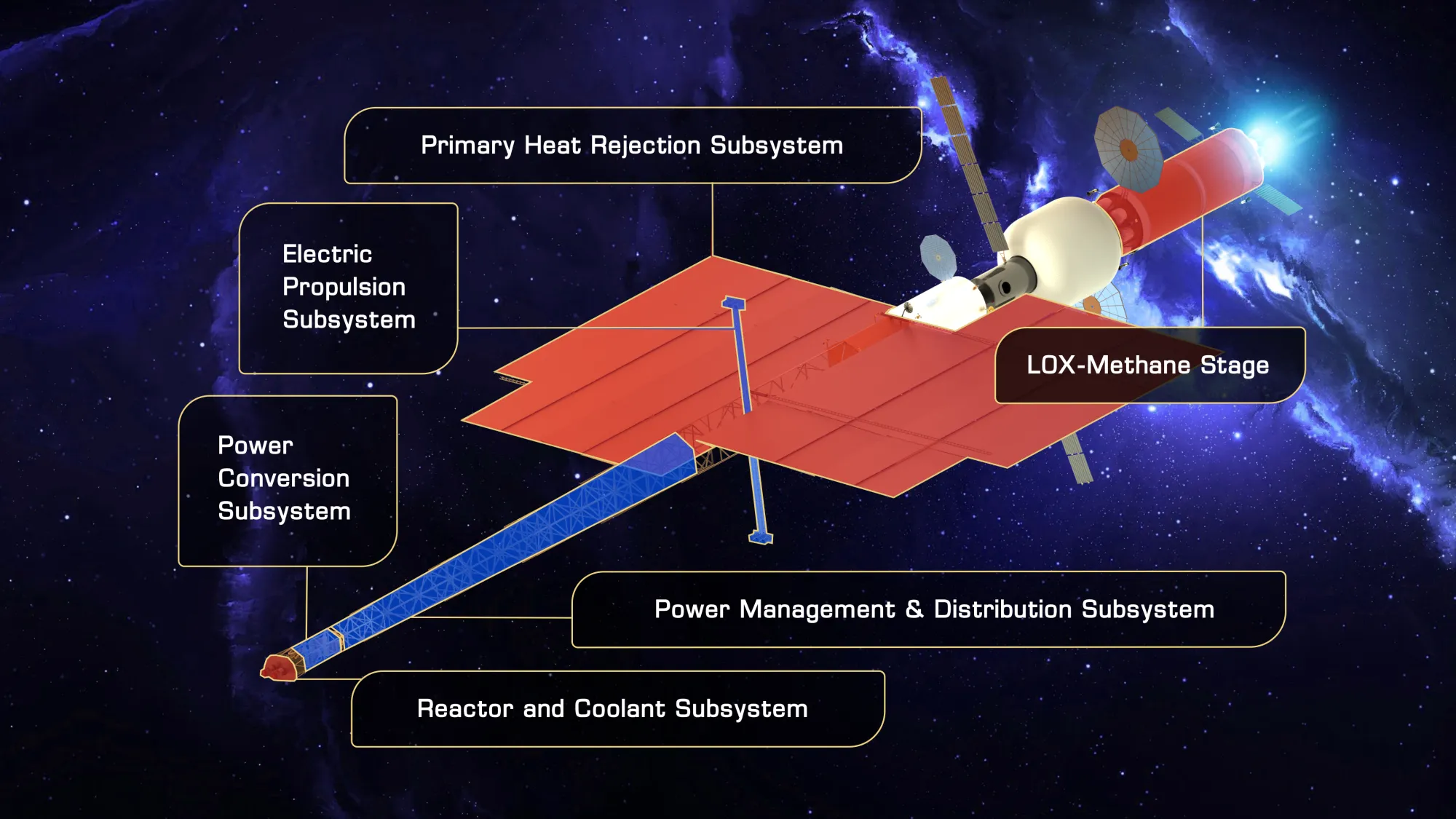
This efficiency-versus-thrust trade-off highlights why nuclear electric propulsion might be ideal for long-duration missions where time is less critical than fuel conservation. While chemical rockets typically achieve specific impulse values of 300-450 seconds, ion thrusters can reach 3,000-5,000 seconds—making them extraordinarily fuel-efficient but with thrust levels thousands of times lower.
"Then there's Nuclear Thermal Propulsion, like DARPA's DRACO (Demonstration Rocket for Agile Cislunar Operations) program," Nix continues, referring to one of the most advanced current efforts to develop nuclear thermal propulsion. In July 2023, DARPA awarded contracts to Lockheed Martin, Blue Origin, and General Atomics for the program's first phase. "It takes hydrogen, flows it through a nuclear reactor to superheat it, and then uses it as propellant—giving massive thrust without chemical reactions or many moving parts beyond pumps."
These technologies offer 2-5 times the efficiency of chemical rockets, potentially revolutionizing transit times between Earth and the Moon and enabling more dynamic operations in cislunar space. But when will they be ready?
"For timelines, a demonstration rocket for either approach could be ready by the end of this decade," Nix projects. "For operational systems, particularly human-rated ones with nuclear power, we're looking at the mid-2030s to early 2040s. The technology is nearly ready, but developing safe, scaled systems takes time."
As the Agile Space Operations Software Branch Chief, how are you addressing the unique challenges of developing and maintaining software for space systems, particularly in terms of reliability, security, and the ability to update systems in orbit?
"At Space CAMP, our vision is to revolutionize the U.S. Space Force digital landscape through mission-enhancing software solutions, innovative development practices, and strengthening strategic partnerships," Nix explains, describing a transformation in how military space software is conceived and implemented. "We're addressing these challenges in two different ways."
The first approach tackles legacy systems that weren't designed for today's rapidly evolving threat landscape. "We're moving legacy ground systems off servers and physical hardware, updating the code base to run in the cloud. This provides a modern architecture while reducing the physical footprint for hardware."
His second strategy addresses the traditionally slow pace of military procurement. "We're addressing the long timeline of traditional acquisition processes, which can take years to field systems. We identify gaps by speaking directly with operators, then rapidly develop prototypes to close those gaps and assist with refining requirements within the larger Joint Requirements Oversight Council acquisition framework."
This framework plays a critical role in how military space capabilities evolve. The Joint Requirements Oversight Council (JROC) is a high-level Department of Defense body chaired by the Vice Chairman of the Joint Chiefs of Staff, which validates capability requirements for major defense acquisition programs.
Nix's approach represents a paradigm shift in space software architecture: "In the past, we built monolithic control systems for individual satellites. Now we're building microservices and moving to cloud platforms, which enhances security by creating boundary layers around applications while using platforms inherently structured to be safe."
This microservices architecture—where applications are broken into small, independent services that communicate through well-defined APIs—contrasts with traditional monolithic space systems where all functionality exists in a single codebase. For space applications, this offers distinct advantages, as Nix explains:
"For maintainability, this approach lets us maintain small pieces of code without taking down entire systems. We can test specific components, run them through the pipeline to verify requirements, deploy them, and if issues arise, quickly revert to previous working versions."
When asked about the progress of this transformation, Nix is candid: "This transition is currently about half complete. Legacy systems like military satellites, GPS, and others are gradually migrating to the cloud, with both contractual and technical factors influencing the pace."
Drawing from your work on the Minotaur rocket programs, what technical advancements in launch vehicle design do you believe are necessary to support the deployment of larger, potentially nuclear-powered spacecraft?
"When I worked on Minotaur and tracked developments in launch vehicles, we used to be very mass-limited—it cost thousands of dollars per pound to launch," recalls Nix, referring to his experience with the Minotaur rocket family. Developed originally by Orbital Sciences (now part of Northrop Grumman), these launch vehicles repurpose decommissioned ICBM motors combined with commercial upper stages to create cost-effective launch solutions. Since its first launch in 2000, the Minotaur series has conducted over 25 missions with high reliability, primarily serving government and defense customers.
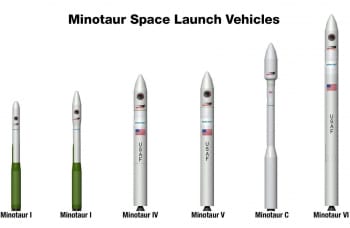
The landscape has changed dramatically, according to Nix: "Now with SpaceX's Falcon, ULA's Vulcan, and other larger launch vehicles coming online, we're no longer mass-bound."
This evolution has particularly significant implications for nuclear systems. "Space Nuclear was always limited by weight due to radiation shielding materials like tungsten or uranium for the core," Nix explains. Tungsten, with the highest melting point of any metal (3,422°C) and excellent radiation attenuation properties, provides superior radiation protection but at approximately twice the density of lead—introducing significant mass challenges. "With today's heavy-lift capabilities, that constraint is diminishing. Instead, we're now limited by fairing volume and the complexities of deployable structures needed for nuclear-powered spacecraft."
The new challenges are more complex than simply lifting mass to orbit, Nix elaborates: "The heat management systems for nuclear power have intricate plumbing to move heat throughout the system and to the radiators. Packaging these systems and developing reliable deployment mechanisms for complex structures is the challenge we're working to solve."
Looking to the future, Nix describes another paradigm shift on the horizon: "We're also researching assembly in orbit with commercial partners and industry, which allows us to launch components separately and assemble them in space rather than launching complete systems. This shift means that instead of being mass-limited, we're now more volume-limited and focused on the complexity of deployment mechanisms."
With your background in materials engineering and work on advanced materials for aircraft, what novel materials or manufacturing techniques do you believe hold the most promise for improving spacecraft thermal management and radiation shielding?
"As we've researched this effort, AFRL sees a need to operate at higher temperatures, both in the reactor and thermal management systems," Nix begins, outlining a crucial materials challenge. "Current terrestrial reactors operate near 800°C, but we'd like to develop space systems operating at 1400°C to make them more compact and improve the energy-to-mass ratio. To reduce radiator size, we need higher temperature radiators (500-600°C)."
These extreme requirements push beyond conventional materials, as Nix explains: "These advancements drive us toward refractory metals like nickel alloys and other exotic materials."
The refractory metals he references represent a special class of materials characterized by extraordinary resistance to heat and wear. The principal refractory metals—niobium, molybdenum, tantalum, tungsten, and rhenium—all exhibit melting points above 2000°C, making them indispensable for extreme-temperature applications.
"Matching thermal expansion coefficients is critical for optimizing heat flow," Nix continues, highlighting the complex engineering challenges involved. "The transition to pumped sodium-potassium liquid heat transfer also shows promise."
This sodium-potassium (NaK) liquid metal alloy serves as a remarkable heat transfer medium that remains liquid from -12.6°C to 785°C at atmospheric pressure—ideal for high-temperature space nuclear applications without requiring the high pressures of water-based systems. The drawback, which Nix doesn't mention but would be familiar with, is NaK's extreme reactivity—it ignites spontaneously on contact with air and reacts explosively with water, necessitating completely sealed systems.
NaK: Sodium-Potassium Liquid Alloy. Synthesis and Reactions
Beyond materials themselves, Nix is particularly excited about new manufacturing approaches: "One of the bigger manufacturing techniques we're exploring with AFRL's Materials Directorate and industry partners is additive manufacturing of metal alloys combined with AI to optimize designs. This approach is yielding new, innovative material configurations that perform as well or better than traditional designs while using less material, weighing less, and sometimes being manufactured faster."
The AI-driven design process Nix describes is producing counter-intuitive results that challenge conventional wisdom: "When we use AI to develop shapes for additive manufacturing, we sometimes get designs that—according to textbook engineering principles—shouldn't work. But when we manufacture and test these AI-designed components, they often perform better than expected because the computers identified solutions we didn't consider."
Nix views this man-machine partnership as transformative rather than threatening: "Right now, AI is a tool we use to find new approaches to traditional design challenges, helping us use materials more efficiently and create lighter components that can be manufactured faster."
How might the commercialization of space, particularly through companies developing nuclear technologies for space applications, affect traditional geopolitical power dynamics and potentially create new forms of resource competition?
"I think anytime a new technology or application of terrestrial technology enters the space domain, it affects the global space dynamic," Nix observes, considering the broader implications of the commercial space revolution. "Commercial entities are changing the game in space, with their rapid adoption of new technologies driving innovation to gain competitive edges."
Regarding nuclear technologies specifically, Nix sees resource competition as inevitable: "With nuclear technology specifically, resource competition will focus on materials that go into these systems—whether beryllium oxide for reflectors, high-temperature nickel alloys, advanced electronics, or the rare earth metals used in manufacturing these components."
Beryllium oxide, which Nix mentions as a reflector material for reactors, combines exceptional thermal conductivity with electrical insulation properties. In nuclear applications, it serves as both an effective neutron moderator and reflector, though it presents significant manufacturing challenges due to toxicity when inhaled as dust particles.
The rare earth elements (REEs) he references comprise a set of 17 metallic elements critical for advanced electronics, powerful permanent magnets, lasers, and precision guidance systems used in space technology. China currently dominates global REE production and processing—controlling approximately 85% of the world's supply—creating strategic concerns for aerospace and defense applications.
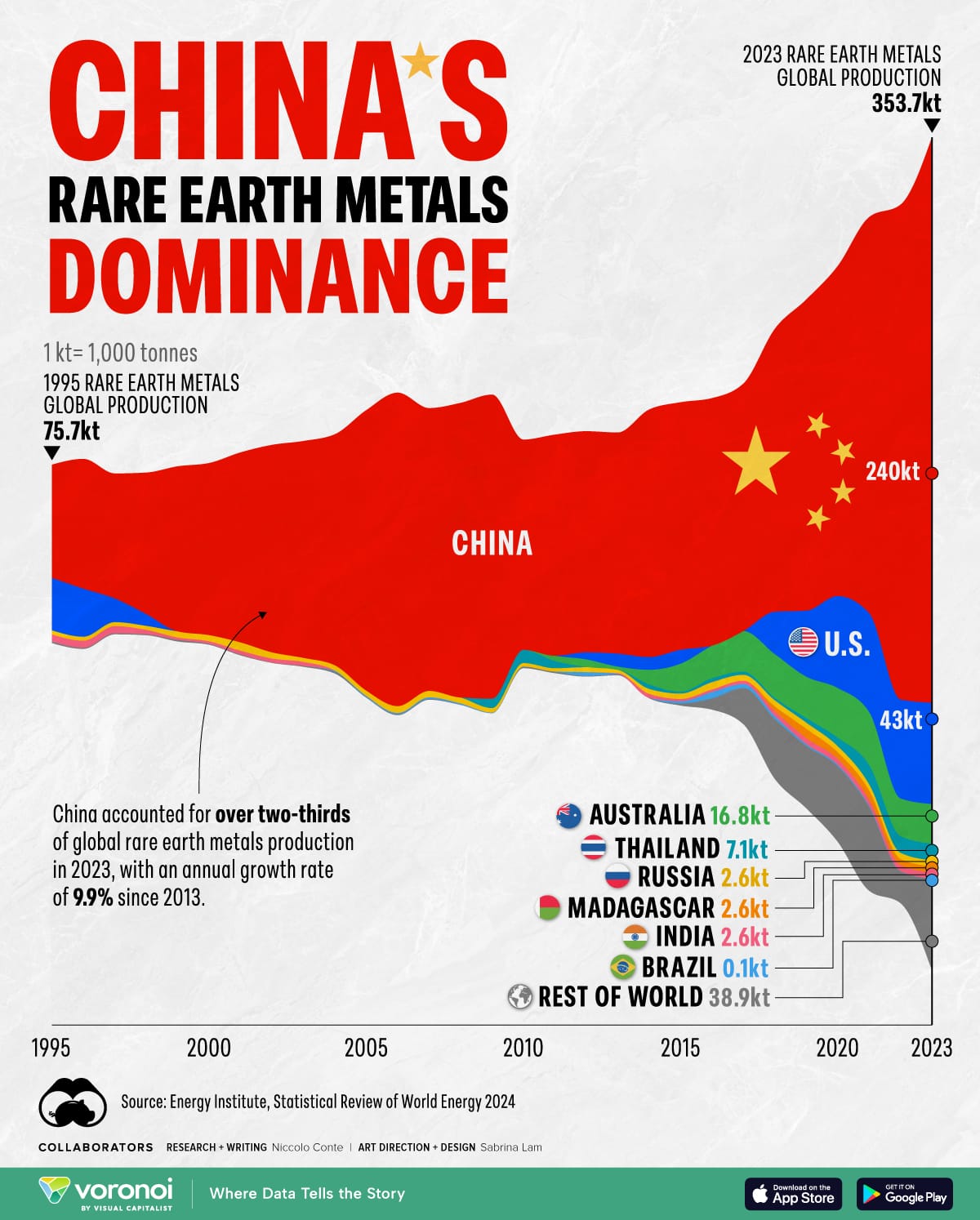
"While commercial space itself may not directly affect traditional geopolitical power dynamics, how governments and commercial entities use these new capabilities will drive changes in power relationships," Nix continues, distinguishing between the technology itself and its application. "As we commercialize more of space, companies will compete with nation-states for the same resources."
This blurring of lines between commercial and government activities raises new security questions, as Nix explains: "This also raises questions about protection: what is our obligation as a department to protect our nation's resources in orbit, even when they're commercial rather than DoD assets? How should these commercial assets be protected if something happens to them?"
Reflecting on his career, Nix marvels at the industry's transformation: "Over my 20-year career in space, I've seen remarkable growth—from 30-40 launches globally per year to thousands annually." This growth trajectory mirrors the dramatic expansion of commercial space activities, with the global space economy reaching an estimated $546 billion in 2022 according to the Space Foundation. "The investments in money, resources, and talent are driving innovation at an unprecedented pace. It's truly motivating to work on new applications of technology, including repurposing terrestrial technologies for space environments."
About Thomas Nix
Lieutenant Colonel Thomas Nix, United States Space Force, JETSON Project Lead and Senior Military Advisor, Spacecraft Technology Division (RVS), Air Force Research Laboratory( AFRL), Kirtland AFB, New Mexico. As Senior Military Advisor, Lieutenant Colonel Nix provides leadership and direction for over 120 personnel (24 Military, 100 Civilians) conducting world class research across multiple portfolios to advance spacecraft technologies and oversight of a $125M annual budget across 33 technology programs. As JETSON, program lead, Lt Col Nix provides oversight for $70M program advancing multiple technical areas including heat dissipation, power conversion, and nuclear power systems.
Lt Col Nix graduated from the United States Air Force Academy and earned his commission in 2002. He began his career at Specialized Undergraduate Pilot Training (SUPT) at Laughlin AFB, TX as a student pilot. Assignments following that include at Materials Directorate and Headquarters, Air Force Research Laboratory, Wright-Patterson Air Force Base where he worked on advanced ceramics, polymers, and multiple aircraft material upgrades for F-22, JSF, C-17, RQ-4, and A-10. He also was the AFRL program lead for rapid runway expansion testing, USAF Body/Vehicle Armor Subject Matter Expert, and the Executive Officer for the AFRL Commander during his tenure.
Following that assignment, Lt Col Nix transferred to Vandenberg AFB, CA where he worked on the initial Minotaur IV rocket launch along with 12 additional Minotaur I/IV launches, and Group and Wing staff rotations, Then, he transferred to Los Angeles AFB, CA; where he was the Requirements Chief for the Global Positioning System (GPS) enterprise, balancing 4 ACAT- I program requirement changes and leading a $255M Systems Engineering support source selection. Following that assignment, he was selected as technical lead for the Multi-Int Fusion Processing System and Sentient Operations Branch Chief at the National Reconnaissance Office in the Ground Enterprise Division. There he oversaw the development and execution of $238M/year budget and lead the transformation of Intelligence Community processing to the cloud and the adoption of Machine Learning and Artificial Intelligence to enhance the National Overhead Systems Future Ground Architecture. Later, he transferred to Kirtland AFB, NM to lead the advanced analytics division at the Air Force Inspection Agency as well as deploying to Camp Arifjan, Kuwait as the Inspector General and Chief of External Oversight for Combined Joint Task Force-Operation Inherent Resolve before transferring to his current assignment in AFRL.